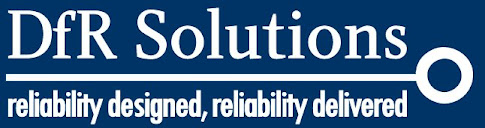
Wednesday, August 31, 2011
Thermal Uprating
Using a component above its rated temperature is always challenging (and surprisingly common). In this white paper, DfR provides a concise explanation of uprating, including the risks, the costs, and the process. For more component-specific guidance, visit our White Paper web page. For more information on our uprating and derating services, please contact Gregg Kittlesen, gkittlesen@dfrsolutions.com.
Tuesday, August 30, 2011
True Root-Cause Analysis (RCA)
The staff at DfR Solutions performs over 400 failure investigations every year. What differentiates DfR from all the others? We know true root cause analysis. As detailed in this illustrating report, DfR surpasses other organizations by using unparalleled combination of equipment, electrical characterization, and knowledge of manufacturing methods and semiconductor physics. For more information on how we can take your organization to the next level, please contact Tom Johnston, tjohnston@dfrsolutions.com.
Labels:
DFR Solutions,
Jim McLeish,
root cause analysis,
Tom Johnston
Saturday, August 27, 2011
Sherlock Automated Design Analysis Tool Expanding Rapidly
The response of the electronics community to DfR's new Automated Design Analysis™ tool has been overwhelming. Since the launch of Version 2.0, over one hundred licenses have been issued and demand continues to rise. TRW is just one of many satisfied customers. Interested? Contact us at sales@dfrsolutions.com and learn how you can be a part of a design revolution.
Labels:
ADA,
automated design analysis,
DFR Solutions,
Sherlock,
TRW
Friday, August 26, 2011
RoHS Part II Finally Arrives
The new RoHS Directive became law on July 21, 2011. Key points:
- No new restricted substances
- Nine (9) exclusion categories - military, space, transportation (trains, planes, autos), fixed installation, large industrial tools, off-road machinery (i.e., bulldozers), implantable devices, solar panels, and R&D equipment
- Compliance timeline - medical and monitoring/control have 3 years, in-vitro medical has 5 years, and industrial monitoring/control has 6
- Exemptions will end in 5-7 years, including telecom and high lead
- CE mark required
- Larger companies must go beyond certificates of compliance
- Your EU importer is now also liable
- Oh, and don't forget India
Labels:
Cheryl Tulkoff,
Craig Hillman,
DFR Solutions,
ROHS,
RoHS II,
ROHS2
Friday, August 12, 2011
Design for ESD & ESD Failure Analysis on Aug 18th at 3pm
2011 TX ESD ASSOC Event
Why Design for ESD Prevention?
Aug 18, 2011 at 3pm - Design for ESD and ESD Failure Analysis Techniques
3M Innovation Center
The foundation of a reliable product is a robust design which provides margin, mitigates risk from defects, and satisfies the customer. Ensuring reliability of electronic designs is becoming increasingly difficult due to:
• Increasing complexity of electronic circuits
• Increasing power requirements
• Introduction of new component and material technologies
• Increasing power requirements
• Introduction of new component and material technologies
• Introduction of less robust components
This results in multiple potential drivers for failure. While most companies are acutely aware of the hazards of ESD (electrostatic discharge), few are aware of just how pervasive ESD failures actually are.
Join us for this presentstion and see what you need to do or learn more about. Presentation geared for engineers and manufacturing personnel who need to learn more and understand design for ESD prevention and how it applies to their individual applications.
There is no charge for attending however we do ask you to RSVP with your name, company, phone and email for badging and planning purposes. Your information is not given outside the Texas ESD Association except to 3M security to make badges.
RSVP to Ray Bowman [rayb1721@yahoo.com]
For more information regarding Texas ESD Association activities, please go to the following
Labels:
Cheryl Tulkoff,
DFR Solutions,
ESD,
failure analysis
Subscribe to:
Posts (Atom)