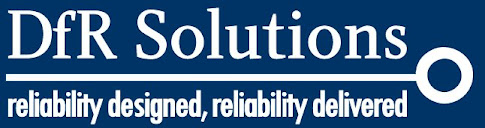
Tuesday, May 31, 2011
Field Failure Early Warning Systems (EWS)
Monday, May 30, 2011
Package on Package: DfM / DfR, Part 1
Friday, May 27, 2011
Cheryl Tulkoff Appears on Riverwood Solutions TV
While at IPC APEX 2011, Cheryl Tulkoff appeared on Riverwood Solutions TV to explore the challenges facing product reliability as a result of the move to a more outsourced solution to manufacturing. Riverwood Solutions helps OEMs improve supply chain performance, optimize their operations & maximize the value of their outsourced relationships. |
Thursday, May 26, 2011
DfR Solutions in Harrisburg, PA: May 31-June 2
Tuesday, May 24, 2011
How to Design for Thermal Cycling Webinar: Tuesday, May 24
Monday, May 23, 2011
Electronic Equipment Reliability & Test Seminar -MET Labs (Austin, TX: May 24)
Friday, May 20, 2011
Motherboard Expert Anne Drees Joins DfR Solutions
Anne spent eight years at Dell, where she led teams that designed, created, and delivered high-end motherboard solutions. Being on the frontlines of new technology, Anne has debugged silicon, circuit and software issues. Since being with Dell Computer, Anne has created custom engineering solutions for clients in a diverse range of industries. Anne's strengths in problem solving stem from her sharp analytical skills and methodical approach. Anne has a B.S. in Electrical and Computer Engineering from Carnegie Mellon. Contact her at adrees@dfrsolutions.com.
Sunday, May 15, 2011
DfR Solutions Supports NSF-funded Energy Research Program with Best Practices in Solar Technology
Greg Caswell will provide a guiding hand on Solar Packaging and Manufacturability.
DfR Solutions, a leader in quality, reliability, and durability (QRD) solutions for the electronics industry, is very proud to announce that Greg Caswell, Senior Member of the Technical Staff, has been nominated to the Advisory Board of the National Science Foundation (NSF) funded Vertically Integrated Center for Transformative Energy Research (VICTER), a multi-campus center consisting of the University of Arkansas, University of Arkansas at Little Rock (UALR), Arkansas State University, and University of Arkansas Pine Bluff.
Greg Caswell has been a leading figure in electronics packaging and manufacturing for over 25 years, from being the primary author of the first book on manufacturing of surface mount electronics to his more recent role as President of the International Microelectronics and Packaging Society (IMAPS).
“It is a distinct pleasure to support the students and faculty as they develop their implementation strategies and further the leading edge of solar energy,” said Mr. Caswell. “There are a number of synergies between traditional electronics and newer technologies, such as solar and light emitting diodes (LEDs), that will allow me to use my background in electronic packaging, particularly from a reliability perspective, to help provide insight into their advanced development activities. I look forward to working with such a talented group of individuals.”
“Mr. Caswell is a packaging expert and a long acquaintance of mine through IMAPS,” explained Professor Ajay Malshe, the Executive Director of Materials and Manufacturing Research Laboratories and coordinator of VICTER’s research activities at the University of Arkansas.” VICTER is honored to welcome Greg Caswell as a member of our advisory board who will bring an industrial perspective to this strategic area for success of the center, as packaging of solar devices connects the sun to a reliable energy grid. His extensive experience in electronics packaging will make him a valuable asset to our mission.” “Mr. Caswell and our entire External Advisory Board serve an invaluable role for our center in that they have a broad perspective on the field and can help ensure that VICTER’s research efforts are relevant and focused and that we are aware of other opportunities for collaborations and partnering,” said Alan Mantooth, VICTER’s Executive Director.
Wednesday, May 11, 2011
DfR Solutions Expands Into Design for Supportability (DfS)
To respond to increasing demands from its customers for a broader capability in product support and systems lifecycle engineering for complex systems, DfR Solutions, a leader in quality, reliability, and durability (QRD) solutions for the electronics industry, is proud to announce the hiring of Walt Tomczykowski as Vice President.
Walt arrives at DfR after a renowned career at ARINC, where he used his extensive experience and reliability knowledge to assist his numerous government and commercial customers in successfully meeting their lifecycle management and product support goals. He brings a diverse systems engineering experience into DfR, with activities in investigating the early use of plastic encapsulated microcircuits (PEMS) in harsh DoD environments, improving the reliability of numerous DoD weapon systems, performing engineering assessments of commercial aviation landing systems to determine the impact of R&M on integrity and continuity of service, and calculating reliability analyses on positive train control systems for the railroad industry. These successes resulted in improving the reliability of products and systems while reducing total ownership costs.
“We are very excited at becoming the first full-service, organization to combine Design for Reliability (DfR), Design for Manufacturing (DfM), and now Design for Supportability (DfS) into a comprehensive Design for Excellence (DfX) program,” said Dr. Craig Hillman, CEO of DfR Solutions. “Because of his expertise, Walt is uniquely qualified to leverage DfR’s existing capabilities at material, component, board, module, and box level into robust assessments, solutions, and predictions for complex systems managed under a variety of sustainment configurations. We have already found that Walt’s unique combined background of reliability, life cycle management, obsolescence and counterfeit parts mitigation to be extremely valuable to wide variety of markets, including telecommunication, medical, transportation, and alternative energy.”
“I joined DfR Solutions because their focus of helping people design-in reliability is exactly what is needed in this era of reduced budgets and cost efficiencies,” said Tomczykowski. “At DfR Solutions, I can apply my systems life cycle engineering expertise obtained from a broad range of industries to help OEMs, integrators, and end users. By expanding DfR Solutions into supportability, we can now help our clients address this critical element during design which ultimately lowers total ownership costs.”
DfR Solutions recognizes that the decisions made early in the design and development process greatly impacts the ultimate life cycle costs. By including design for supportability into a comprehensive design for excellence approach that includes DfR and DfM, it will drive the creation of more reliable and supportable products, delivered on time with lower life cycle cost.
About DfR Solutions, LLC: DfR Solutions has world-renowned expertise in applying the science of Reliability Physics to electrical and electronics technologies and is a leading provider of quality, reliability, and durability (QRD) research and consulting for the electronics industry. The company’s integrated use of Physics of Failure (PoF) and Best Practices provides crucial insights and solutions early in product design and development and throughout the product life cycle. DfR Solutions specializes in providing knowledge- and science-based solutions to maximize and accelerate the product integrity assurance activities of their clients in every marketplace for electronic technologies (consumer, industrial, automotive, medical, military, telecom, oil drilling, and throughout the electronic component and material supply chain). For more information regarding DfR Solutions,visit www.dfrsolutions.com.
Thursday, May 5, 2011
Learn How to Design for Thermal Cycling!
SAVE THE DATE: May 24, 2011 12-1pm EDT and 8-9pm EDT Learn How to Design for Thermal Cycling. Attend this informative webinar presented jointly by IMAPS and DfR Solutions, a leading provider of quality, reliability, and durability research and services for the electronics industry.
Modern electronic design is highly complex. Changes in temperatures, thermal cycling, will eventually cause materials joined together to pull apart. Good design will delay this event as long as possible. In this webinar, Dr. Nathan Blattau will:
• Review the fundamental drivers for thermo-mechanical fatigue • Using Physics of Failure, relate drivers to predictive algorithms • Demonstrate how to develop more robust designs against thermal cycling environments
Don’t miss out! Early Bird Registration here. Click here to view the newest webcast on Sherlock - the
|
Wednesday, May 4, 2011
Austin Electronic Equipment Reliability & Testing Seminar: May 24th
May 24, 2011 I. Test Plan Development
|
II. The new test methodology for Radiated Emissions Testing (above 1GHz) to EN55022:2006+A1:2007 (Information Technology Equipment- Radio Disturbance Characteristics- Limits and Methods of Measurement). Previous versions of EN55022 did not require radiated emission testing above 1GHz. This new version of EN55022 specifies REE testing up to 6 GHz. Test methodology is also significantly different from FCC/ANSI C63.4 requirements. The new version requires testing to be done using a validated test site (chamber) according to CISPR 16-1-4. This session will cover the changes in the new version with a special emphasis on free space emissions requirements. III. The Synergy Between Reliability and Safety in IT Equipment Regulatory, business and public constraints require a thorough understanding of the physics of how electronics fail and the tools and methodologies available to meet all customer expectations. This session will use the experience of industry experts and lessons learned to provide guidance on how the selection and control of design, materials, and processes to ensure an optimum level of product reliability also positively impacts safety. IV. Quality, Reliability & Durability for Industrial Applications This presentation will describe a process that can be followed by the design engineer to ascertain the impacts of the operational and environmental stresses over the life cycle of a product. Examples will be shown of how the effects of thermal cycling, shock and vibration affect the solder joint fatigue, PTH fatigue, CAF resistance and overall reliability. Plus MET will provide a hands-on demonstration in the 10m chamber for EMC troubleshooting! MET Laboratories' electro-magnetic compatibility (EMC) laboratory has extensive experience in testing a wide range of commerical and military equipment for the domestic and global marketplace. DfR Solutions is world-renowned for its expertise in applying the science of Reliability Physics to electrical and electronics technologies, and the company is a leading provider of quality, reliability, and durability (QRD) research and consulting for the electronics industry. Directions to MET Austin: 35N or 35S Parmer Exit East on Parmer Left at 1st light on McCallen Pass Go pass big Dell building on right (13301 B) Next building on right is MET (13301) |