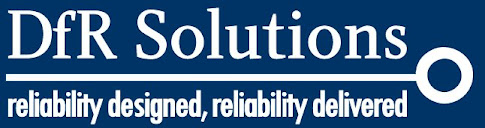
Wednesday, November 24, 2010
DfR's Craig Hillman an invited speaker at IPC Tin Whiskers Conference
8:30 am–12:00 pm
Causes of Tin Whiskers: Theories of Formation
Craig Hillman, Ph.D., CEO, DfR Solutions
This workshop will help provide an understanding of fundamental drivers for tin whiskers: how they can be related to presence/absence and growth rates under a variety of environmental conditions. Discussions will focus on current theories on tin whisker initiation and growth: a review of material diffusion, stress gradients, oxide formation and how various plating elements and environments play a critical role in these behaviors.
General trends in research from exposing tin plating to a variety of environments (temperature, humidity, vibration, mechanical shock, corrosion, pressure, bending) will be reviewed and related back to drivers. The ability to test for and predict the occurrence of tin whiskers will be presented, with a critical review of existing tin whisker prediction algorithms and the risk/benefit of implementing these equations into design decisions and reliability predictions.
Your Instructor
Craig Hillman, Ph.D. is CEO and managing partner of DfR Solutions. Dr. Hillman's expertise includes best practices in design for reliability (DfR), lead-free strategies, supplier qualification for commodity and engineered products, passive component technology, and printed board failure mechanisms. Dr. Hillman holds two patents, has published more than 50 white papers, and has appeared in more than 40 publications; he has presented on a wide variety of reliability issues to over 250 organizations. A member of the Lead-Free Electronics Risk Management (PERM) working group and invited lead-free SME on the DoD Lead-Free Manhattan Project (LFMP), Dr. Hillman has a BS in metallurgical engineering and material science from Carnegie Mellon a doctorate in materials from UC-Santa Barbara, and took his post-doctoral fellowship at Cambridge University.
Tuesday, November 16, 2010
Defibrillators Failing Too Early and Too Often
Engineering Design Practices.
Review of past recalls suggests that manufacturers of external defibrillators sometimes use design practices that lead to inconsistent device performance. In one example, a firm designed its voltage-monitoring circuit to draw power from the same power source it was intended to monitor. Because of this design, a momentary drop in the voltage caused a false signal to shut down the AED and the device was unable to deliver a shock, which may have caused a patient’s death. In another case, a firm used the wrong kind of component in one of the circuits, causing the device to be susceptible to interference from noise coming from the device’s power line. Good engineering design practices also require user interfaces (like dials, monitors, alarms, and connectors) meet users’ needs. Recent surveys suggest that improvements in user interfaces may be warranted.
Manufacturing Practices.
The FDA’s analysis of recalls and inspections identified problems in how manufacturers test and incorporate components used in the manufacture of external defibrillators, as well as how they evaluate changes to the device before they are implemented to assure that device modifications do not adversely impact the safety and effectiveness of the technology. Between 2005 and 2010, the FDA issued nine warning letters to external defibrillator manufacturers, seven of which cited the firms for failing to appropriately control these aspects of their manufacturing process.
In several cases, manufacturers purchased components from suppliers who did not meet the manufacturers’ required specifications. In some cases, the problem with the component was due to a change in how the component was manufactured by the supplier. However, it is the manufacturer’s responsibility to assure that the components it receives meet its specifications.
Design and Manufacturing are two key areas where DfR can help your company prevent problems! For more information, please contact Cheryl Tulkoff, ctulkoff@dfrsolutions.com.
Wednesday, November 10, 2010
DfR White Paper: 0201 and 01005 Adoption in Industry
0201 and 01005 components have grown to represent a large portion of the modern component market and usage will continue to increase as time goes on. Currently, issues with manufacturability, cost of use, and inspection limit wider adoption of these components. The trend for smaller products in certain industries will drive an increase in adoption that will necessarily result in improved practices in manufacturing. As the market matures, and more reliability data becomes available, even those applications where reliability is paramount will begin to see adoption of these small parts. Indeed, the majority of respondents to DfR Solutions’ survey expect to be using 0201 components within the next three years.
Interested in learning more? Contact Cheryl Tulkoff, ctulkoff@dfrsolutions.com
Saturday, November 6, 2010
DfR at IPC Tin Whiskers Conference in Chicago, IL: December 6-7
Craig Hillman has been invited to give a half-day workshop on Tin Whisker Prediction and a half-day workshop on Tin Whisker Mitigation and Risk Assessment at this unique industry conference focused on practical methodologies. For more information or to arrange a meeting during the conference, please contact Craig Hillman, chillman@dfrsolutions.com.
Friday, November 5, 2010
DfR Solutions Presents at IPC High Reliability Workshop
Cheryl Tulkoff, Senior Member of the Technical Staff, will be presenting "Solving Problems with Reliability, Repair and Rework in the Lead-Free Era" at IPC's High Reliability Workshop on December 8, 2010, in Santa Clara, California.
This session addresses potential reliability issues within lead-free processes, current state of industry knowledge and risk mitigation based on product design, materials, complexity, volumes and customer expectations of reliability. The session summary includes a roadmap for ensuring the reliability of lead-free product.
For more information or to register, please visit the IPC event website.
Thursday, November 4, 2010
DfR at IPC / SMTA Cleaning Conference - Chicago, IL: November 16-18
DfR Solutions will be presenting on a number of topics at the IPC / SMTA Cleaning industry conference in Chicago on November 16th through the 18th. Randy Schueller, rschueller@dfrsolutions.com, will provide updates on sulfur attack of silver and other board platings. Seth Binfield, sbinfield@dfrsolutions.com, will present on recent work on flux chemistry and voiding, performed in collaboration with Jeannette Plante of NASA's Goddard Space Flight Center.
Wednesday, November 3, 2010
Shock and Vibration of Pb-free
DfR has announced it is building upon its successful SBIR Phase I Partnership Program. Where SBIR Phase I Partnership focused on capturing the behavior of Pb-free solder under shock and vibration, the SBIR Phase II Partnership will focus on quantifying the value of various mitigation strategies, including staking, underfill, dummy ball / ball removal, and cutouts. Participants will not only have exclusive access to the largest investigation into Shock and Vibration of Pb-free solder ever performed, they will also finally be able to capture the cost / risk tradeoffs necessary for a successful product launch. For more information, please contact Craig Hillman, chillman@dfrsolutions.com.
Tuesday, November 2, 2010
Say Goodbye to Reliability?
Taiwan's Contract Electronics Manufacturers to Benefit from Freer Outsourcing Atmosphere. For a long time, Intel, which commands over 80% of world's market for computer microprocessors, has demanded notebook-computer manufacturers using its microprocessors to build the processors packed with its designated wireless-network modules into their notebook computers. Five Taiwanese CMs can now choose their own modules for inclusion. Will they chose the most reliable or will they choose the least expensive? With the margins the way they are for CMs, this is not a tough question. What does that bode for notebook computers? Ask Cheryl Tulkoff, ctulkoff@dfrsolutions.com.