The copper revolution has reached component packaging (just in time for 3D integration!). Copper wirebonds and copper pillars are proliferating like wildfire throughout multiple platforms. Copper is cheaper than gold, but has lower resistance. What's not to like? However, with every material change come potentially unknown risks. Copper wirebonds require special atmospheres, higher bonding forces, and changes in bond pad dimensions. The need for palladium plating can also drive galvanic corrosion. Copper pillars can increase the risk of white bump, drive complete consumption of solder to intermetallic at elevated temperatures, and increase stress states during thermal cycling. For more information, contact Craig Hillman, chillman@dfrsolutions.com.
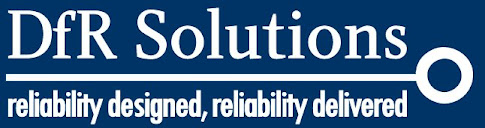
Subscribe to:
Post Comments (Atom)
No comments:
Post a Comment